Whether you're planning a small home improvement or a large-scale commercial development, understanding the cost per yard of concrete is crucial. The price of concrete varies depending on factors like location, type of mix, and delivery logistics. On average, homeowners and contractors can expect to pay between $120 and $150 per cubic yard, but this can fluctuate based on specific project requirements. By breaking down the cost factors and exploring ways to optimize expenses, you can make informed decisions and ensure your project stays within budget. Knowing the cost per yard of concrete is not just about the upfront price—it’s also about understanding the long-term value it brings to your project. Concrete is durable, low-maintenance, and offers excellent structural integrity, making it a cost-effective choice despite its initial expense. However, hidden costs such as labor, reinforcement materials, and transportation can add up quickly. To avoid surprises, it’s essential to factor in all these elements before finalizing your budget. By doing so, you’ll have a clearer picture of the total investment required and can allocate resources more efficiently. This article dives deep into the intricacies of the cost per yard of concrete, answering common questions and providing actionable insights. From exploring what influences pricing to offering tips on reducing costs without compromising quality, we’ve got you covered. Whether you’re a DIY enthusiast or a seasoned contractor, this guide will equip you with the knowledge to navigate the complexities of concrete pricing and make smarter financial decisions for your next project.
Table of Contents
- What Factors Influence the Cost Per Yard of Concrete?
- How Does Concrete Type Affect Pricing?
- What Are the Hidden Costs of Concrete Delivery?
- Is It Possible to Reduce the Cost Per Yard of Concrete?
- Why Location Matters in Concrete Pricing?
- How Can You Estimate the Total Cost of Your Concrete Project?
- What Are the Best Practices for Buying Concrete in Bulk?
- Frequently Asked Questions About Cost Per Yard of Concrete
What Factors Influence the Cost Per Yard of Concrete?
Several key factors contribute to the cost per yard of concrete, and understanding them is essential for budgeting effectively. The type of concrete mix you choose plays a significant role. For example, standard ready-mix concrete is generally more affordable than specialized mixes like fiber-reinforced or high-strength concrete. These specialized mixes are designed for specific applications, such as withstanding heavy loads or resisting environmental damage, which can drive up the cost. Additionally, the inclusion of additives like accelerators, retarders, or air-entraining agents can also affect the price.
Another critical factor is the delivery logistics. If your project site is located far from the batching plant, transportation costs can add significantly to the overall expense. Delivery charges typically include fuel costs, driver wages, and truck maintenance. Moreover, if the site is difficult to access due to narrow roads or other obstacles, additional fees may apply. It’s also worth noting that the time of year can influence pricing. For instance, concrete prices tend to rise during peak construction seasons when demand is high, making it essential to plan your project strategically.
Read also:Explore The Best Features Of Videos Com Your Ultimate Guide
Finally, labor costs and preparation work are often overlooked but can make a substantial difference. Pouring and finishing concrete requires skilled labor, and the complexity of the project will dictate how much time and effort is needed. Factors like site preparation, formwork, and reinforcement installation can all impact the final cost. By accounting for these elements upfront, you can avoid unexpected expenses and ensure your project runs smoothly.
How Does Concrete Type Affect Pricing?
The type of concrete you select has a direct impact on the cost per yard of concrete. Standard ready-mix concrete is the most common choice for residential and small commercial projects. It’s affordable, easy to work with, and suitable for general purposes like driveways, sidewalks, and foundations. However, if your project requires enhanced durability or specific performance characteristics, you may need to opt for a more specialized mix, which can increase the cost per yard of concrete.
For instance, high-strength concrete is designed to withstand heavy loads and is often used in commercial buildings, bridges, and industrial facilities. This type of concrete contains additional cement and specialized aggregates, making it more expensive than standard mixes. Similarly, fiber-reinforced concrete incorporates synthetic or steel fibers to improve tensile strength and reduce cracking, making it ideal for projects like pool decks or industrial floors. While these mixes offer superior performance, they come at a premium price.
Another factor to consider is decorative concrete, which is used for aesthetic purposes. Stamped, stained, or colored concrete can transform ordinary surfaces into visually appealing features, but the added materials and labor required for installation can significantly increase costs. Ultimately, the choice of concrete type should align with your project’s functional and aesthetic requirements while staying within your budget.
What Are the Hidden Costs of Concrete Delivery?
When calculating the cost per yard of concrete, it’s easy to overlook the hidden costs associated with delivery. One of the most significant factors is the distance between the batching plant and your project site. Longer distances mean higher fuel costs and longer drive times, both of which can increase the overall expense. Additionally, if your site is located in a remote or hard-to-reach area, you may incur extra charges for special equipment or extended delivery times.
Another hidden cost is the potential for delays. Concrete is a time-sensitive material that must be poured before it begins to set. If unforeseen circumstances like traffic, weather, or logistical issues cause delays, it could result in wasted material or additional labor costs. To mitigate these risks, it’s crucial to coordinate closely with your supplier and ensure that all preparations are in place before the delivery arrives. This includes having the site ready, formwork installed, and labor on hand to handle the pour efficiently.
Read also:Who Played Bane In The Dark Knight Rises Meet The Actor Behind The Mask
Finally, don’t forget about disposal fees. If your project generates excess concrete or requires removal of old materials, you’ll need to account for disposal costs. These fees can vary depending on local regulations and the volume of material being disposed of. By factoring in these hidden costs upfront, you can create a more accurate budget and avoid unpleasant surprises down the line.
How Can You Minimize Delivery-Related Expenses?
To reduce delivery-related costs, consider scheduling your concrete delivery during off-peak hours. This can help you avoid traffic congestion and ensure a smoother, faster delivery process. Additionally, consolidating your orders into larger batches can often result in discounted rates from suppliers. Finally, ensure that your project site is easily accessible to minimize the need for specialized equipment or additional labor.
Is It Possible to Reduce the Cost Per Yard of Concrete?
Reducing the cost per yard of concrete is not only possible but also practical with the right strategies. One effective approach is to shop around and compare quotes from multiple suppliers. Prices can vary significantly between companies, so taking the time to research and negotiate can yield substantial savings. Additionally, consider purchasing concrete in bulk if your project requires a large volume. Bulk orders often come with discounts, which can lower the overall cost per yard of concrete.
Another way to save is by optimizing your project timeline. Scheduling your concrete pour during the off-peak season can result in lower prices, as demand is typically lower during these periods. You can also save on labor costs by planning your project efficiently and minimizing downtime. For example, having all necessary materials and equipment on-site before the delivery arrives can help streamline the process and reduce the need for overtime pay.
Finally, consider using alternative materials or methods to reduce costs. For instance, replacing a portion of the cement in the mix with fly ash or slag can lower expenses without compromising quality. These supplementary cementitious materials are often cheaper and can improve the durability of the concrete. By exploring these options, you can achieve significant cost savings while maintaining the integrity of your project.
What Are Some Cost-Saving Alternatives to Traditional Concrete?
Exploring alternative materials can be a game-changer when trying to reduce the cost per yard of concrete. For example, lightweight concrete uses expanded clay or shale aggregates, which are less dense and therefore cheaper to transport. Similarly, pervious concrete, which allows water to pass through, is an eco-friendly option that can reduce the need for additional drainage systems. These alternatives not only lower costs but also offer unique benefits that can enhance your project.
Why Location Matters in Concrete Pricing
The cost per yard of concrete can vary significantly depending on your location. In urban areas, where demand for construction materials is high, prices tend to be higher due to increased competition and logistical challenges. Conversely, rural areas may offer lower prices but could incur higher transportation costs if the nearest batching plant is far away. Understanding the local market dynamics is essential for accurate budgeting and cost management.
Regional differences in raw material availability also play a role. For example, areas with abundant natural resources like sand and gravel may have lower concrete prices, while regions that rely on imported materials will likely see higher costs. Additionally, local regulations and taxes can impact pricing. Some areas impose environmental fees or require specific certifications, which can add to the overall expense.
To navigate these variations, it’s advisable to consult with local suppliers and industry experts. They can provide valuable insights into regional pricing trends and help you identify cost-saving opportunities. By tailoring your approach to the specific conditions of your location, you can optimize your budget and ensure a successful project outcome.
How Can You Estimate the Total Cost of Your Concrete Project?
Estimating the total cost of your concrete project involves more than just calculating the cost per yard of concrete. Start by determining the volume of concrete you’ll need. This can be done by measuring the dimensions of the area to be poured and converting them into cubic yards. Once you have this figure, multiply it by the average cost per yard of concrete in your area to get a rough estimate.
Next, factor in additional costs such as labor, formwork, reinforcement, and finishing. Labor costs can vary depending on the complexity of the project and the skill level of the workers. Formwork and reinforcement materials like rebar or wire mesh are essential for structural integrity and should be included in your calculations. Finishing costs, such as stamping or staining, should also be accounted for if you’re planning a decorative concrete project.
Finally, don’t forget to include a contingency budget for unexpected expenses. This can cover anything from material shortages to weather-related delays. By taking a comprehensive approach to cost estimation, you’ll be better prepared to manage your budget and ensure a successful project outcome.
What Are the Best Practices for Buying Concrete in Bulk?
Buying concrete in bulk can lead to significant cost savings, but it requires careful planning and execution. One of the first steps is to accurately estimate the volume of concrete you’ll need. Overestimating can result in wasted material, while underestimating can lead to delays and additional costs. Use precise measurements and consult with your supplier to ensure you order the right amount.
Another best practice is to negotiate pricing with your supplier. Bulk orders often qualify for discounts, so don’t hesitate to ask for a better rate. You can also inquire about loyalty programs or long-term contracts, which may offer additional savings. Additionally, consider scheduling your delivery during off-peak hours to reduce transportation costs and avoid delays.
Finally, ensure that your project site is fully prepared before the delivery arrives. This includes having all necessary equipment and labor on hand to handle the pour efficiently. By following these best practices, you can maximize your savings and ensure a smooth, cost-effective process.
Frequently Asked Questions About Cost Per Yard of Concrete
What is the Average Cost Per Yard of Concrete?
The average cost per yard of concrete typically ranges from $120 to $150, depending on factors like location, mix type, and delivery logistics.
How Can I Save Money on Concrete Costs?
You can save money by comparing quotes from multiple suppliers, purchasing in bulk, and scheduling deliveries during off-peak seasons.
Does the Type of Concrete Affect the Price?
Yes, specialized mixes like high-strength or fiber-reinforced concrete are more expensive than standard ready-mix concrete due to their enhanced performance characteristics.
Conclusion
Understanding the cost per yard of concrete is essential for any construction
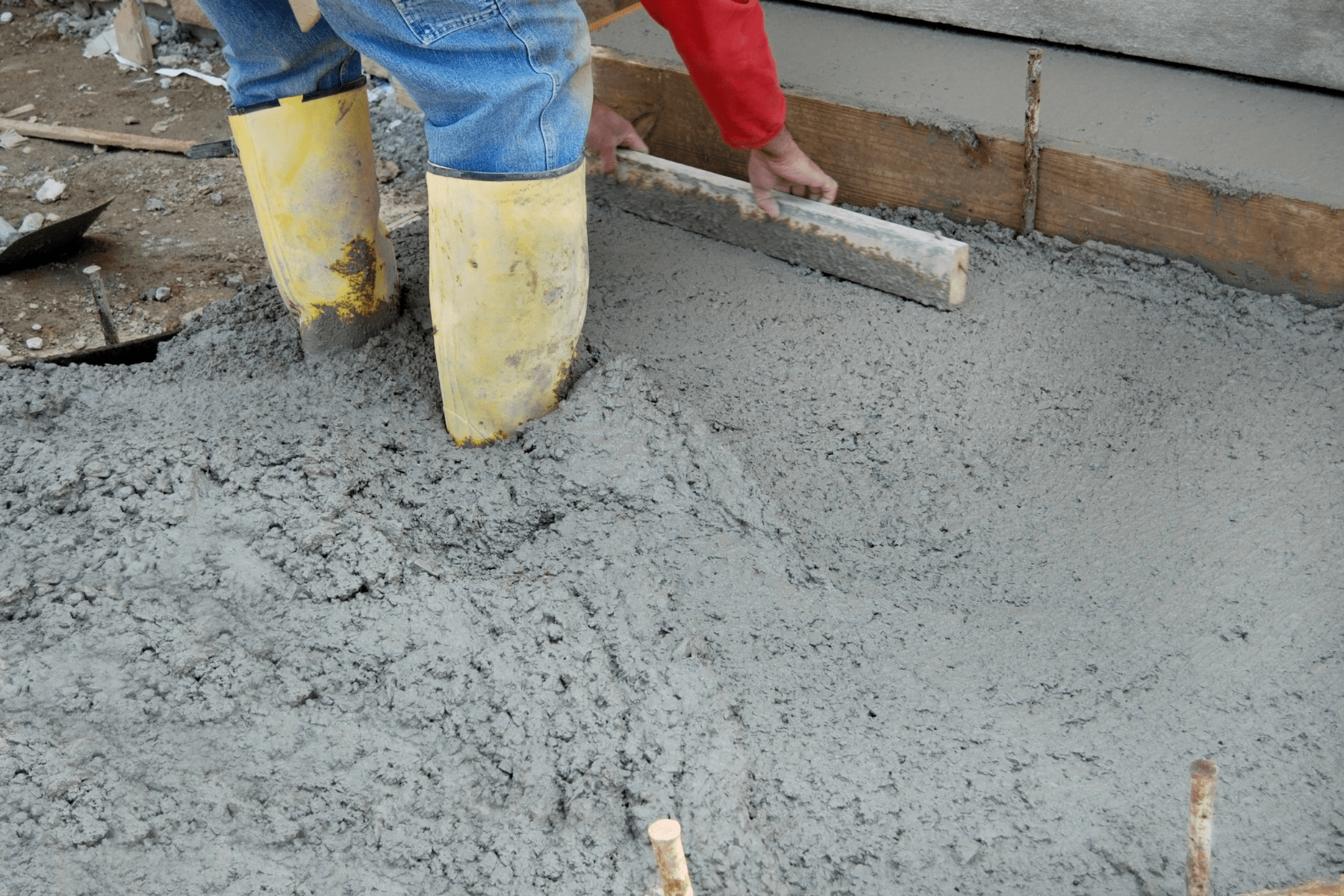
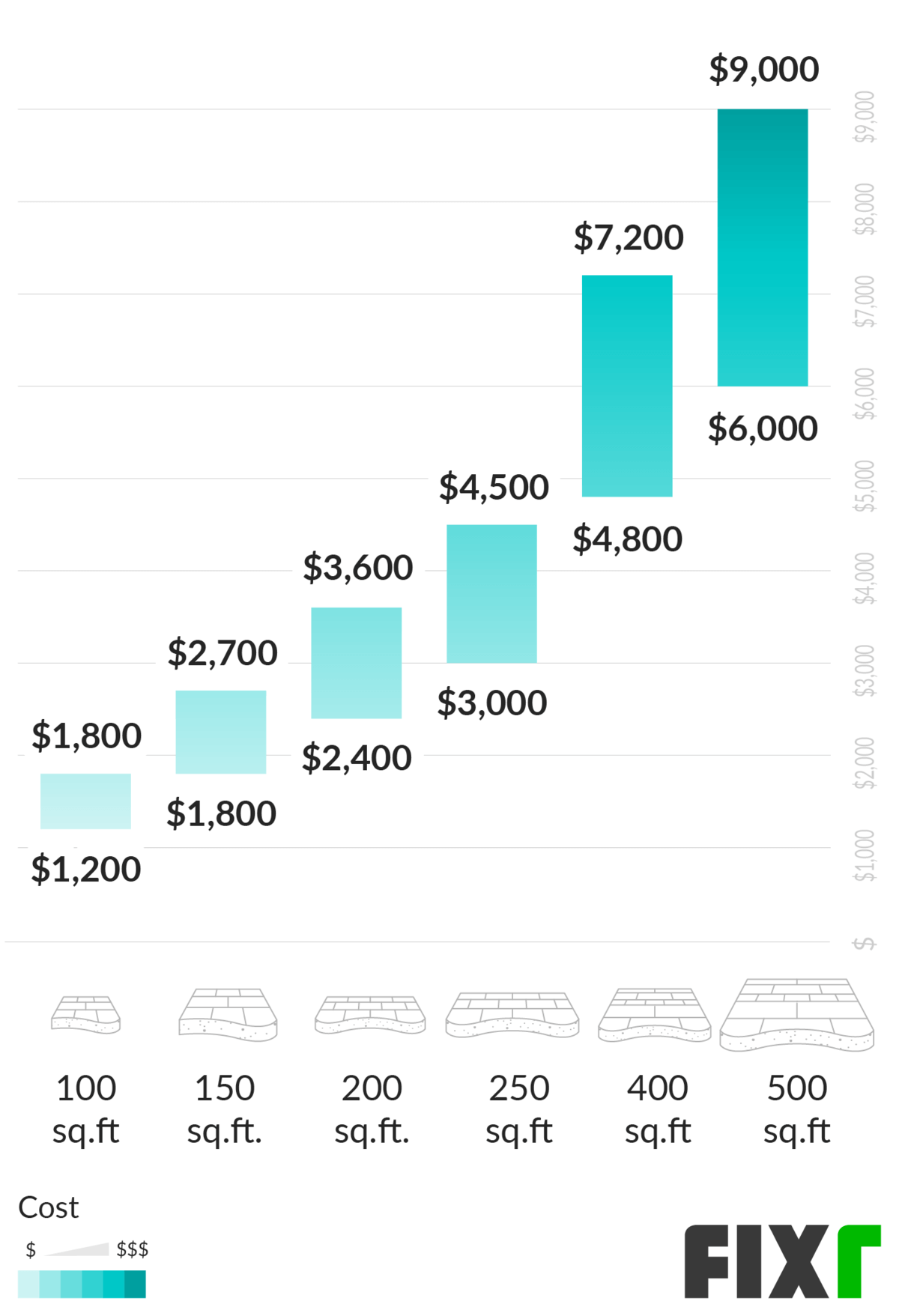